0 引言
钢轨焊接是铺设无缝线路的前提和基础,是高速铁路轨道工程建设的关键技术。随着我国高速铁路与城市轨道交通的快速发展,为确保列车安全平稳运行,对钢轨的焊接质量提出了更高的要求。本标段使用国产YHG-1200TH型移动式闪光焊机,将500 m长钢轨焊接成无缝线路。钢轨焊接过程主要包括闪平阶段、脉动阶段、过渡阶段、连续阶段、加速阶段、顶锻阶段和保压阶段。合同要求钢轨焊接接头(简称接头,以下同)的探伤检测执行TB/T 1632.1—2014《钢轨焊接 第1部分:通用技术条件》和TB/T 2658.21—2007《工务作业 第21部分:钢轨焊缝超声波探伤作业》标准。焊轨施工时业主提出,接头探伤检测要采用更为严格的Q/CR 707—2019《固定式钢轨闪光焊接》标准。
1 问题的提出
本标段待焊接钢轨为U71MnG热轧钢轨和U71MnH热处理钢轨,采用移动式闪光焊机进行焊接。首先将线路上铺设的500 m长钢轨焊接成1 000~2 000 m的单元轨节,完成应力放散锁定后,再将单元轨节焊接成跨区间无缝线路,共需要焊接约2 800个接头。根据业主提出的要求,焊筋要求全断面打磨平整,实现了“焊缝不可见”,在消除接头表面应力集中的同时,也排除了接头表面不平顺对探伤扫查的干扰,避免将缺陷波视同为焊筋波,造成漏探。
在钢轨焊接过程中,接头探伤不合格的情况在不同焊机、焊接不同轨种时呈现出一定的规律性:在焊轨施工初期,1号焊机焊接U71MnG热轧钢轨时接头伤损大部分集中在轨底、U71MnH热处理钢轨接头伤损集中在轨腰断面的中心区域;在焊轨施工后期,2号焊机焊接U71MnG热轧钢轨时接头伤损大部分集中在轨下颚部位。
对于探伤不合格接头必须锯切重焊,完成应力放散锁定后的无缝线路,若接头探伤不合格,锯切重焊严重影响施工进度,大幅增加施工成本。因此,需要分析缺陷产生的机理和规律性,从设备、工艺等方面进行排查,制订针对性的措施,提高接头质量,减少探伤不合格接头的数量,从而降低重焊的成本。
2 问题分析及措施
2.1 设备性能的影响
在焊轨施工初期,统计分析1号焊机探伤报警(探伤发现异常波或超标不合格)的接头,探伤报警的接头和焊接记录曲线的异常密切相关,多数探伤报警的接头焊接记录曲线在焊接末期(加速阶段)出现小电流或提前短路。统计探伤报警接头(热轧钢轨)30个,其中5个接头焊接记录曲线正常,16个接头焊接记录曲线在加速阶段出现小电流(电流低至接近断路),2个接头焊接记录曲线发生提前短路,3个接头焊接记录曲线加速阶段小电流和提前短路同时存在,4个接头焊接记录曲线钢轨消耗量偏低,分别是26.7,27.5,28.0,28.3 mm, 正常情况下钢轨消耗量在32 mm左右。其中,小电流导致的探伤报警占比约63%,且缺陷大部分位于轨底。
选取典型焊接记录曲线进行分析,如图1~3所示。
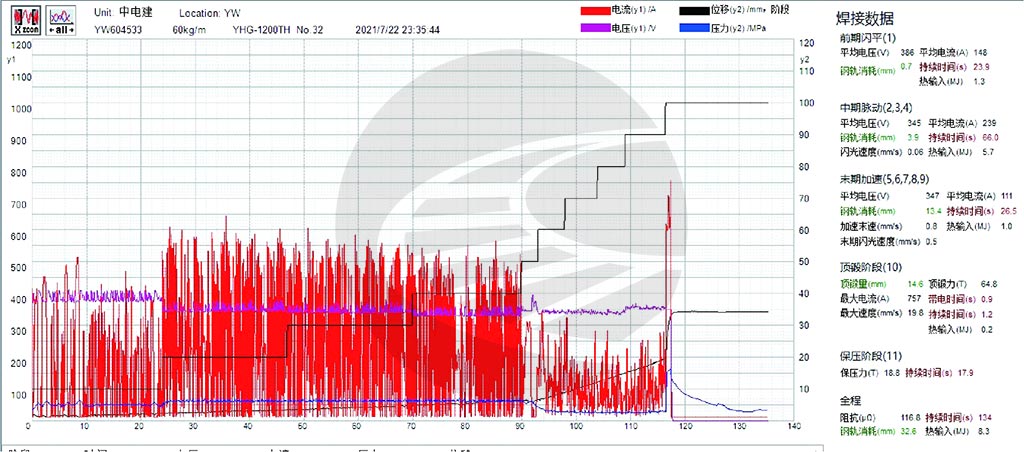
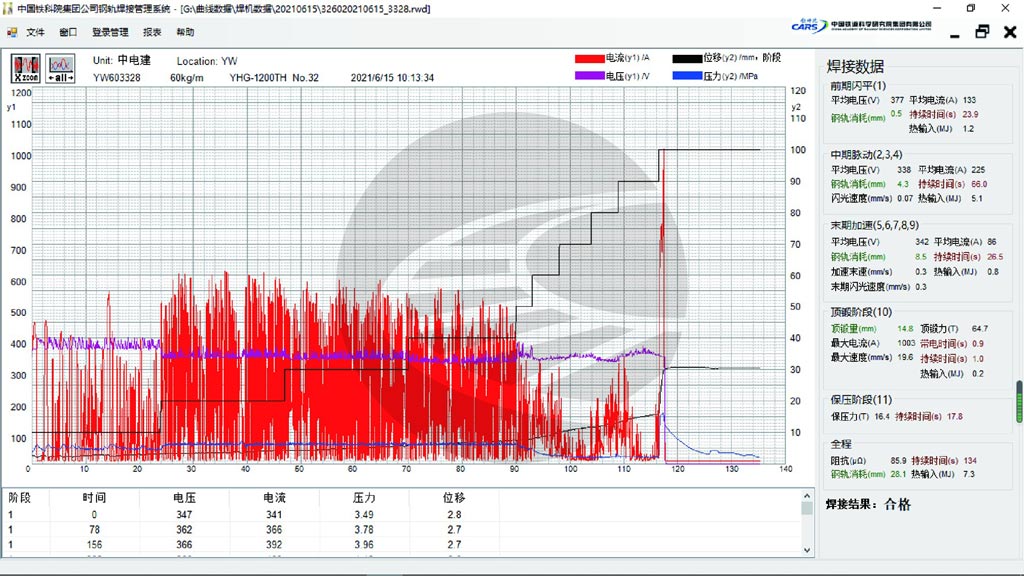

图1所示是正常的焊接记录曲线,在加速阶段保持相对激烈的闪光,提供充分的保护气氛;在带电顶锻阶段短路电流和顶锻位移曲线同步。图2焊接记录曲线中加速阶段的闪光速度下降,末期出现小电流,焊接过程中会看到明显的闪光中断,即类似于“断闪”的现象,同时钢轨的焊接消耗量偏低。图3焊接记录曲线中存在提前短路现象,在带电顶锻前出现大电流,此时焊机动架处于加速送进的末期,提前过渡到带电顶锻阶段,导致实际带电顶锻时间长于工艺规范的设定值。对比以上3种典型的焊接记录曲线可知,在焊接工艺参数保持不变的情况下,焊机动架的送进动作出现明显迟滞或提前,说明焊机的位移控制系统存在问题。出现该情况后,通过现场调查发现在出现伤损的焊轨施工区段,焊机附近存在较大功率电气设备运转,如使用大功率报话机通话、施工区域相邻线路列车通过等情况,处于静止状态的焊机,其动架和静架实际相对位移应显示为零,但观察控制界面的位移显示值却出现明显的变化。比如在打开报话机通话时,位移示数会快速增加,容易产生图3所示提前短路的焊接记录曲线。
通过反复试验,判断焊机电气性能不稳定,抗干扰能力较差,在外界干扰下,比例伺服阀放大板零位漂移,影响焊接过程。其中反向零位漂移会产生图2所示的小电流焊接记录曲线,小电流无法提供充分的焊接保护气氛,容易在焊接末期产生各种焊接缺陷。而正向零位漂移会产生图3所示的提前短路焊接记录曲线。
比例伺服阀及其对应的比例伺服阀放大板是闪光焊机的核心控制部件,控制焊接时焊机动架和静架间的位移,包括焊接初期的送进分离、焊接后期的加速烧化及末期的顶锻动作。在进行焊机性能测试时,若比例伺服阀放大板在零位时,动架不应前进或后退。动架处于静止状态时,位移显示值应保持恒定。
针对以上情况,采取增加可靠的接地、优化比例伺服阀、比例伺服阀放大板壳体和屏蔽电缆的接线方式等措施,提高控制系统的抗干扰能力,同时在焊接过程中避免使用大功率报话机通话、临线有列车通过时停止焊接作业等,以上措施实施后,比例伺服阀放大板零位漂移导致的以上2类异常焊接记录曲线数量大幅减少,接头的探伤合格率明显提升。
2.2 热处理钢轨的焊接
1号焊机在某区段焊轨施工伤损统计显示,钢轨材质为U71MnG,接头探伤合格率是98.6%(合格接头数量/生产接头数量);钢轨材质为U71MnH,接头探伤合格率是96.5%;另一个区段的U71MnH,接头探伤合格率降低至90.0%。伤损接头对应的焊接记录曲线均正常,和之前热轧钢轨探伤缺陷发生的位置不同,热处理钢轨的缺陷大部分位于钢轨截面中心线距轨顶面65~160 mm不等的轨腰区域,轨腰缺陷均能满足TB/T 2658.21—2007和TB/T 1632.1—2014标准对探伤的要求,却不能满足Q/CR 707—2019的要求。
查阅热处理钢轨相关资料,为了提高钢轨的淬透性,热处理钢轨在冶炼过程中要添加一定数量的合金元素,参照TB/T 2344.1—2020标准附录C,出现伤损的轨腰区域是钢铸坯的中心,是Mn, Si偏析等铸造缺陷集中出现的位置。
基于上述分析,优化接头的焊后热处理工艺,热处理最高温度从900 ℃提高至910 ℃,取得一定效果。将接头进行二次热处理后的效果更为明显,即将探伤超标的接头重新加热到900 ℃以上。以3个接头为例,CTS1003型探伤仪显示1#接头的超标异常波位于焊缝中心距轨顶面约140 mm处,缺陷反射为Ф3-6 dB(探伤灵敏度为增益78 dB,以下同);2#接头的超标异常波位于焊缝中心距轨顶面约150 mm处,缺陷反射为Ф3-6 dB;3#接头的超标异常波位于焊缝中心距轨顶面约150 mm处,缺陷反射为Ф3-7 dB。通过对3个接头进行二次热处理,复探全部合格,波幅均下降2~3 dB。
二次热处理可以消除因局部晶粒粗大导致的探伤异常,但对于轨腰的探伤异常,二次热处理对其改善有限,其影响机理有待做进一步的研究。
2.3 钢轨母材对探伤的影响
钢轨探伤标准和接头探伤标准存在不对等的问题,按照接头探伤标准对探伤报警接头相邻的钢轨母材进行探伤扫查,发现2例钢轨母材超标,1例位于轨头部位,缺陷反射达Ф3-2 dB,距熔合线约55 mm; 1例位于轨腰部位,缺陷反射达Ф3-3 dB,距熔合线约63 mm。YHG-1200TH型焊机采用脉动闪光焊工艺,焊接热影响区宽度约40 mm, 正火后的热影响区宽度约80 mm。尽管母材探伤超标属于较低概率事件,但探伤扫查热轧钢轨和热处理钢轨,后者的杂波和异常波明显多于前者的。
国内有轨底夹杂物超标影响焊接的案例,若母材探伤超标的现象达到一定的比例,就要从源头上控制钢轨的合金元素含量与偏析和夹杂物水平,同时在进行型式检验时,应优化焊接工艺参数,使其尽可能地适应钢轨材质的波动。
2.4 优化焊接工艺规范
在焊轨施工后期,2号焊机焊接热轧钢轨接头出现多个轨下颚缺陷,一般发生在轨下颚棱角部位,属于表面或浅表缺陷,通过修磨可以消除或降低异常波的波幅,但容易磨亏钢轨母材,不能从根源上彻底解决问题。
2.4.1 理化分析
对缺陷取样镶嵌磨平,部分表现为空隙状缺陷。同时使用电子扫描显微镜(SEM)做形貌观察和成分分析。
图4所示为腐蚀后焊缝缺陷宏观形貌。该样本中,碳烧损形成的白色亮线是钢轨闪光焊独有的特征,亮线中间部位存在比较明显的中断。图5呈现出铁素体网断裂形貌。合金元素面扫描显示:S,Mn元素沿缺陷呈点状聚集,提示缺陷附近有MnS夹杂富集;Cu, Cr, Ni元素分布较均匀,无明显偏聚现象。缺陷处化学成分见表1。
表1 缺陷处化学成分分析结果(质量分数)(%)
C | O | Si | S | Mn | Fe | Cu |
5.20 | 7.66 | 0.70 | 2.44 | 3.91 | 79.53 | 0.56 |
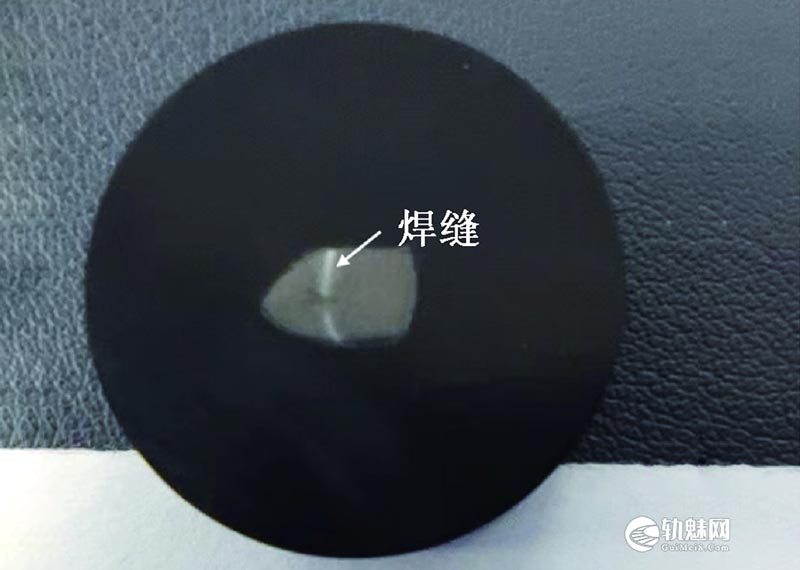
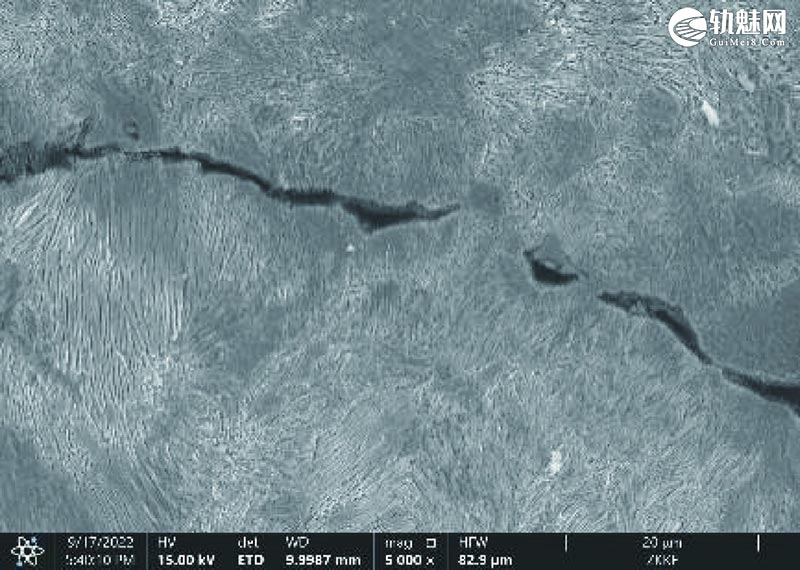
根据TB/T 2344.1—2020标准对钢轨化学成分的检测采取宏观取样计算平均值的方式,表1是使用SEM电镜显示的微观分析结果,反映了合金元素的偏析程度,对缺陷形成的分析具有一定的参考价值。
轨下颚的表面缺陷经人工修磨后呈多个针尖状样貌,其色泽明显异于周围的正常金属组织。腐蚀后的高倍照片呈现出类似裂纹的形态,且该区域夹杂物富集、合金元素含量异常,说明该缺陷属于过烧或微裂纹,是标准不允许存在的有害缺陷。
2.4.2 推凸裂纹的可能性
缺陷位于轨头下颚表面,行业内有许多推凸导致浅表裂纹的案例,通常是由于推凸刀刃磨损严重,推凸时浅表金属受到沿钢轨轴向的较大剪切力,焊缝表面或近表面产生裂纹,一般出现在推凸始端焊筋呈钝角的位置。
修磨推凸刀的廓形,将轨下颚的推凸余量增加到2.5 mm以上,同时延长顶锻后推凸的间隔时间,提高接头在推凸时的热塑性,并减少推凸过程对焊接接头的扰动。措施实施后,对减少轨下颚的探伤缺陷起到一定作用。
2.4.3 焊接工艺参数优化
考虑到夹杂物一般比正常组织的熔点低,如焊缝局部残留过热组织,致使夹杂物在此富集,在凝固过程形成晶间液相,结合强度低,在外力(如推凸)或焊缝残余应力的影响下,或产生微裂纹,或夹杂物聚集造成探伤反射异常。
观察推凸切除的焊筋形态,钢轨两侧轨下颚棱角和轨底中心部位的焊筋明显粗大。钢轨属于非闭合断面,各部位的廓形和厚度不同,不同位置的加热温度与顶锻效果存在差异。由于闪光焊工艺的局限性,导致部分区域不能实现充分顶锻。通常情况下,由于高温金属不能被完全挤出焊缝,接头部分区域残存过热或过烧组织,这也是夹杂物富集的区域。
基于上述思路,对焊接工艺参数进行小幅优化:减少脉动阶段的焊接时间,降低焊接热输入;同时适当提高加速阶段的烧化电压与前进速度,可以有效增加加速阶段的钢轨消耗量,减少局部过热金属的残留。焊接工艺参数微调后,取得了明显效果。周施工探伤合格率统计,一次探伤合格率提升到98%以上,人工修磨的比例也大幅减少。
分析:钢轨内部夹杂物与合金元素偏析往往是形成焊接缺陷的内因,推凸或工艺不当是外因。在焊接前进行型式检验调试焊接工艺参数时,要提高工艺参数的适应性,使其在焊轨生产中能够适应钢轨材质的波动与施工环境的变化;同时,在焊轨施工生产中,焊接工艺参数要根据钢轨材质的波动适当调整,不能一成不变,这也是生产检验的目的之一。
3 结论
接头探伤出现异常波或超标判废,只有当样本积累到一定数量,才能找到其中的规律性,通过分析研判采取相应的措施后,也需要相当的焊轨生产量,才能验证措施是否有效。这需要质量工程师具备一定的判断力,在众多影响因素中识别主要因素,制订具有针对性的改进措施。
设备是工艺的基础,先完善设备性能,后优化工艺规范。在焊轨施工中,若出现批量探伤异常超过正常比例,应做好统计分析,首先要根据焊接记录曲线和焊接数据检查设备状态是否正常;统计缺陷发生的不同部位和频次,参考国内钢轨冶炼水平和行业内焊接缺陷的控制水平,消除设备工装和钢轨母材的影响;在排除上述因素后,认识缺陷性质和产生原因,根据不同工艺规范的加热机理,优化焊接工艺参数,从源头上降低缺陷发生的概率。
(1)比例伺服阀放大板零位等焊机性能参数是保证焊接质量的重要技术指标,在焊轨生产中,应保持稳定,不应出现零位漂移现象。焊机投产时,应关注比例伺服阀放大板的初始零位,投产后定期调整,避免大幅调整影响焊接工艺的稳定性。
(2)随着探伤标准和探伤仪器灵敏度的提高,钢轨母材特别是热处理钢轨存在的夹杂物、合金元素偏析、轧制缺陷等逐渐凸显,是焊接质量不能忽视的重要影响因素。因此,基于钢轨母材的现状,在型式检验环节应重视探伤检测工作,提高工艺参数的适应性或宽泛性,从而提高接头的一次探伤合格率。钢厂应加强对钢轨内部夹杂物与合金元素偏析的控制,提高钢轨的纯净性和均匀性,研究热处理钢轨的焊接性。
(3)关注接头全断面加热区的均匀性,参照国外标准对闪光焊接头热影响区宽度的要求,关注接头在焊态下不同截面的热影响区形态。
(4)接头在轨底或轨下颚出现的探伤报警,如属可视缺陷,即存在微裂纹或过烧风险,无论波幅高低,应打磨彻底消除或做判废处理。
原文出处:
文章来源:钢轨闪光焊接接头内部缺陷原因分析及措施
作者信息:冯继军(中铁三局集团线桥工程有限公司)
期刊信息:焊接技术 . 2025 ,54 (01)