1 概述
北京市轨道交通新机场线(以下简称“新机场线”)是连接北京大兴国际机场与北京市中心城区的轨道交通线路。新机场线南起大兴机场站,途径大兴新城站,北至既有地铁10号线草桥站,线路全长约41.36km(其中路基及高架段长约17.71km,地下段长约23.65km)。新机场线是我国首条设计速度达160km/h的轨道交通线,相较于一般的地铁线,具有行车速度高、环保要求高、下部基础复杂、道床形式多样等特点[3]。
目前,我国城市轨道交通中采用预制板整体道床的有广州地铁4号线(最高速度90km/h)、深圳地铁7号线(最高速度80km/h)、上海地铁18号线(最高速度80km/h)等,其线路环境和设计速度与新机场线差异较大。因此,需要对预制板整体道床的轨道系统进行特殊设计。󠄐󠄹󠅀󠄪󠄣󠄞󠄡󠄤󠄡󠄞󠄤󠄠󠄞󠄢󠄤󠄢󠄬󠅒󠅢󠄟󠄮󠄐󠅅󠄹󠄴󠄪󠄾󠅟󠅤󠄐󠄼󠅟󠅗󠅙󠅞󠄬󠅒󠅢󠄟󠄮󠇘󠆭󠆘󠇙󠆝󠅵󠇗󠆭󠆁󠄐󠇗󠅹󠅸󠇖󠆍󠅳󠇖󠅹󠅰󠇖󠆌󠅹󠄬󠅒󠅢󠄟󠄮
2 普通型预制板整体道床结构
新机场线普通型预制板整体道床设置于有较大沉降危险性的区域(包括地下段和路基段)。
2.1 结构组成
以大兴机场-大兴新城区间为例,地下线道床由上至下的结构组成为:钢轨、弹性分开式扣件、预制轨道板(C60)、隔离层及弹性垫层、限位凹槽、自密实混凝土底座(C40)等。其轨道结构高度为650mm(部分地段为600mm,通过降低自密实底座实现),其中自密实底座高度为202mm(部分地段152mm),轨道板高度为200mm。截面形状见图1。
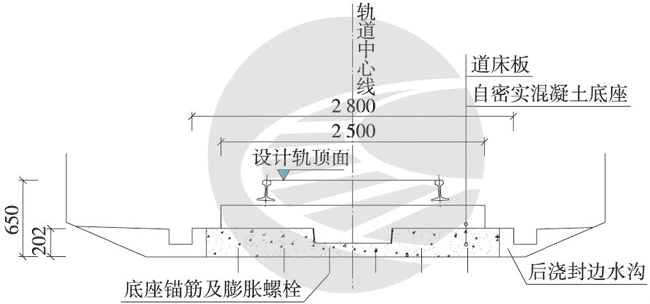
图1 地下线普通型预制板整体道床截面(单位:mm)
路基段道床由上至下的结构组成为:钢轨、弹性分开式扣件、预制轨道板(C60)、隔离层及弹性垫层、自密实混凝土(C40)、限位凹槽、混凝土底座(C40)等。
其轨道结构高度为815mm(至路基表面),其中混凝土底座高度为273mm,自密实混凝土厚度为90mm,轨道板高度为200mm。截面形状见图2。󠄐󠄹󠅀󠄪󠄣󠄞󠄡󠄤󠄡󠄞󠄤󠄠󠄞󠄢󠄤󠄢󠄬󠅒󠅢󠄟󠄮󠄐󠅅󠄹󠄴󠄪󠄾󠅟󠅤󠄐󠄼󠅟󠅗󠅙󠅞󠄬󠅒󠅢󠄟󠄮󠇘󠆭󠆘󠇙󠆝󠅵󠇗󠆭󠆁󠄐󠇗󠅹󠅸󠇖󠆍󠅳󠇖󠅹󠅰󠇖󠆌󠅹󠄬󠅒󠅢󠄟󠄮
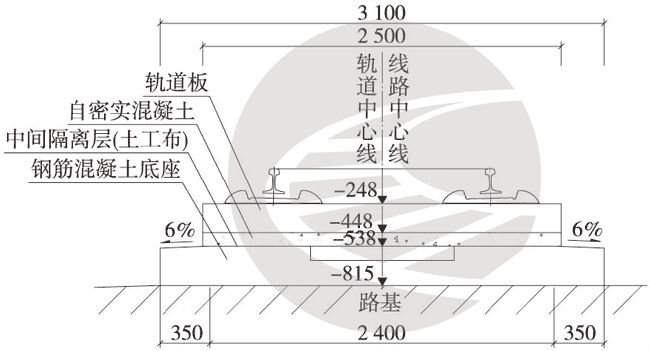
图2 路基段普通型预制板整体道床截面(单位:mm)
2.2 地下线段普通型道床基底结构
(1)自密实混凝土底座顶面距离设计轨顶面448mm。自密实底座与轨道板分块一致。
(2)轨道板尺寸为5300mm×2500mm×200mm(长×宽×高),采用双向先张预应力体系。板与板之间设置宽100mm的板缝。󠄐󠄹󠅀󠄪󠄣󠄞󠄡󠄤󠄡󠄞󠄤󠄠󠄞󠄢󠄤󠄢󠄬󠅒󠅢󠄟󠄮󠄐󠅅󠄹󠄴󠄪󠄾󠅟󠅤󠄐󠄼󠅟󠅗󠅙󠅞󠄬󠅒󠅢󠄟󠄮󠇘󠆭󠆘󠇙󠆝󠅵󠇗󠆭󠆁󠄐󠇗󠅹󠅸󠇖󠆍󠅳󠇖󠅹󠅰󠇖󠆌󠅹󠄬󠅒󠅢󠄟󠄮
(3)轨道板下预制限位凸台。自密实底座采用双凹槽方案,凹槽尺寸为1000mm×700mm×112mm(长×宽×深)。两凹槽中心间距为3.2m。限位凸台上粘贴弹性垫层。自密实混凝土底座和轨道板之间设置4mm厚的隔离层。󠄐󠄹󠅀󠄪󠄣󠄞󠄡󠄤󠄡󠄞󠄤󠄠󠄞󠄢󠄤󠄢󠄬󠅒󠅢󠄟󠄮󠄐󠅅󠄹󠄴󠄪󠄾󠅟󠅤󠄐󠄼󠅟󠅗󠅙󠅞󠄬󠅒󠅢󠄟󠄮󠇘󠆭󠆘󠇙󠆝󠅵󠇗󠆭󠆁󠄐󠇗󠅹󠅸󠇖󠆍󠅳󠇖󠅹󠅰󠇖󠆌󠅹󠄬󠅒󠅢󠄟󠄮
(4)自密实底座于每2块轨道板对应长度设置宽20mm的伸缩缝(伸缩缝材料为聚乙烯泡沫塑料板),并在伸缩缝顶面及两侧采用有机硅酮填缝。󠄐󠄹󠅀󠄪󠄣󠄞󠄡󠄤󠄡󠄞󠄤󠄠󠄞󠄢󠄤󠄢󠄬󠅒󠅢󠄟󠄮󠄐󠅅󠄹󠄴󠄪󠄾󠅟󠅤󠄐󠄼󠅟󠅗󠅙󠅞󠄬󠅒󠅢󠄟󠄮󠇘󠆭󠆘󠇙󠆝󠅵󠇗󠆭󠆁󠄐󠇗󠅹󠅸󠇖󠆍󠅳󠇖󠅹󠅰󠇖󠆌󠅹󠄬󠅒󠅢󠄟󠄮
(5)曲线超高在自密实混凝土底座上实现,采取降低内轨、抬高外轨的方式。󠄐󠄹󠅀󠄪󠄣󠄞󠄡󠄤󠄡󠄞󠄤󠄠󠄞󠄢󠄤󠄢󠄬󠅒󠅢󠄟󠄮󠄐󠅅󠄹󠄴󠄪󠄾󠅟󠅤󠄐󠄼󠅟󠅗󠅙󠅞󠄬󠅒󠅢󠄟󠄮󠇘󠆭󠆘󠇙󠆝󠅵󠇗󠆭󠆁󠄐󠇗󠅹󠅸󠇖󠆍󠅳󠇖󠅹󠅰󠇖󠆌󠅹󠄬󠅒󠅢󠄟󠄮
(6)在自密实混凝土底座外侧二次浇筑双侧水沟,水沟宽200mm,水沟中心线距离线路中心线1600mm,沟底距离设计轨顶面560mm。󠄐󠄹󠅀󠄪󠄣󠄞󠄡󠄤󠄡󠄞󠄤󠄠󠄞󠄢󠄤󠄢󠄬󠅒󠅢󠄟󠄮󠄐󠅅󠄹󠄴󠄪󠄾󠅟󠅤󠄐󠄼󠅟󠅗󠅙󠅞󠄬󠅒󠅢󠄟󠄮󠇘󠆭󠆘󠇙󠆝󠅵󠇗󠆭󠆁󠄐󠇗󠅹󠅸󠇖󠆍󠅳󠇖󠅹󠅰󠇖󠆌󠅹󠄬󠅒󠅢󠄟󠄮
2.3 路基段普通型道床基底结构
(1)混凝土底座的顶面距离设计轨顶面563mm。底座与轨道板分块一致。
(2)轨道板尺寸为5300mm×2500mm×200mm(长×宽×高),采用双向先张预应力体系。板与板之间设置宽136mm或138mm的板缝。󠄐󠄹󠅀󠄪󠄣󠄞󠄡󠄤󠄡󠄞󠄤󠄠󠄞󠄢󠄤󠄢󠄬󠅒󠅢󠄟󠄮󠄐󠅅󠄹󠄴󠄪󠄾󠅟󠅤󠄐󠄼󠅟󠅗󠅙󠅞󠄬󠅒󠅢󠄟󠄮󠇘󠆭󠆘󠇙󠆝󠅵󠇗󠆭󠆁󠄐󠇗󠅹󠅸󠇖󠆍󠅳󠇖󠅹󠅰󠇖󠆌󠅹󠄬󠅒󠅢󠄟󠄮
(3)轨道板下铺设自密实混凝土,设计厚度为90mm,长和宽与轨道板对齐。󠄐󠄹󠅀󠄪󠄣󠄞󠄡󠄤󠄡󠄞󠄤󠄠󠄞󠄢󠄤󠄢󠄬󠅒󠅢󠄟󠄮󠄐󠅅󠄹󠄴󠄪󠄾󠅟󠅤󠄐󠄼󠅟󠅗󠅙󠅞󠄬󠅒󠅢󠄟󠄮󠇘󠆭󠆘󠇙󠆝󠅵󠇗󠆭󠆁󠄐󠇗󠅹󠅸󠇖󠆍󠅳󠇖󠅹󠅰󠇖󠆌󠅹󠄬󠅒󠅢󠄟󠄮
(4)自密实混凝土和混凝土底座采用限位凹槽的方式进行限位,每块轨道板下设两个凹槽,凹槽尺寸为1000mm×700mm×100mm(长×宽×深)。两凹槽中心间距为3.2m。限位凹槽周围设置弹性垫层。自密实混凝土和轨道板之间设置4mm厚的隔离层。󠄐󠄹󠅀󠄪󠄣󠄞󠄡󠄤󠄡󠄞󠄤󠄠󠄞󠄢󠄤󠄢󠄬󠅒󠅢󠄟󠄮󠄐󠅅󠄹󠄴󠄪󠄾󠅟󠅤󠄐󠄼󠅟󠅗󠅙󠅞󠄬󠅒󠅢󠄟󠄮󠇘󠆭󠆘󠇙󠆝󠅵󠇗󠆭󠆁󠄐󠇗󠅹󠅸󠇖󠆍󠅳󠇖󠅹󠅰󠇖󠆌󠅹󠄬󠅒󠅢󠄟󠄮
(5)混凝土底座在现场构筑,于每2块轨道板对应长度设置宽度为20mm的伸缩缝(伸缩缝材料为聚乙烯泡沫塑料板),并在伸缩缝顶面及两侧用有机硅酮填缝。󠄐󠄹󠅀󠄪󠄣󠄞󠄡󠄤󠄡󠄞󠄤󠄠󠄞󠄢󠄤󠄢󠄬󠅒󠅢󠄟󠄮󠄐󠅅󠄹󠄴󠄪󠄾󠅟󠅤󠄐󠄼󠅟󠅗󠅙󠅞󠄬󠅒󠅢󠄟󠄮󠇘󠆭󠆘󠇙󠆝󠅵󠇗󠆭󠆁󠄐󠇗󠅹󠅸󠇖󠆍󠅳󠇖󠅹󠅰󠇖󠆌󠅹󠄬󠅒󠅢󠄟󠄮
(6)曲线超高在混凝土底座上实现,采取抬高外轨的方式。󠄐󠄹󠅀󠄪󠄣󠄞󠄡󠄤󠄡󠄞󠄤󠄠󠄞󠄢󠄤󠄢󠄬󠅒󠅢󠄟󠄮󠄐󠅅󠄹󠄴󠄪󠄾󠅟󠅤󠄐󠄼󠅟󠅗󠅙󠅞󠄬󠅒󠅢󠄟󠄮󠇘󠆭󠆘󠇙󠆝󠅵󠇗󠆭󠆁󠄐󠇗󠅹󠅸󠇖󠆍󠅳󠇖󠅹󠅰󠇖󠆌󠅹󠄬󠅒󠅢󠄟󠄮
3 减振垫浮置板道床(预制板式)
3.1 结构组成
新机场线的减振垫浮置板道床(预制板式)主要设置在大兴新城-草桥区间,其他区间和车站亦有少量设置(为环评单位要求的减振地段)。断面形状为矩形(明挖)及圆形(盾构)。轨道系统的结构组成如下:钢轨、弹性分开式扣件、预制轨道板(C60)、隔离层及弹性垫层、自密实混凝土(C40)、限位凹槽、隔振垫、混凝土底座(C40)等。
对于矩形隧道,轨道结构高度为890mm,其中混凝土底座高度为275mm,隔振垫厚度为27mm,自密实混凝土厚度为90mm,轨道板高度为200mm。对于圆形隧道,轨道结构高度为1000mm,其中混凝土底座高度为435mm,隔振垫厚度为27mm,自密实混凝土厚度为90mm,轨道板高度为200mm。两种断面类型的隧道截面形状见图3、图4。󠄐󠄹󠅀󠄪󠄣󠄞󠄡󠄤󠄡󠄞󠄤󠄠󠄞󠄢󠄤󠄢󠄬󠅒󠅢󠄟󠄮󠄐󠅅󠄹󠄴󠄪󠄾󠅟󠅤󠄐󠄼󠅟󠅗󠅙󠅞󠄬󠅒󠅢󠄟󠄮󠇘󠆭󠆘󠇙󠆝󠅵󠇗󠆭󠆁󠄐󠇗󠅹󠅸󠇖󠆍󠅳󠇖󠅹󠅰󠇖󠆌󠅹󠄬󠅒󠅢󠄟󠄮
- 图3 矩形隧道减振垫浮置板整体道床截面
- 图4 圆形隧道减振垫浮置板整体道床截面
3.2 基底结构
(1)混凝土底座顶面距离设计轨顶面565mm(两种断面隧道相同)。底座与轨道板分块一致。
(2)轨道板尺寸为5300mm×2500mm×200mm(长×宽×高),采用双向先张预应力体系。板与板之间设置宽100mm的板缝。󠄐󠄹󠅀󠄪󠄣󠄞󠄡󠄤󠄡󠄞󠄤󠄠󠄞󠄢󠄤󠄢󠄬󠅒󠅢󠄟󠄮󠄐󠅅󠄹󠄴󠄪󠄾󠅟󠅤󠄐󠄼󠅟󠅗󠅙󠅞󠄬󠅒󠅢󠄟󠄮󠇘󠆭󠆘󠇙󠆝󠅵󠇗󠆭󠆁󠄐󠇗󠅹󠅸󠇖󠆍󠅳󠇖󠅹󠅰󠇖󠆌󠅹󠄬󠅒󠅢󠄟󠄮
(3)轨道板下铺设自密实混凝土,设计厚度为90mm,长和宽与轨道板对齐。󠄐󠄹󠅀󠄪󠄣󠄞󠄡󠄤󠄡󠄞󠄤󠄠󠄞󠄢󠄤󠄢󠄬󠅒󠅢󠄟󠄮󠄐󠅅󠄹󠄴󠄪󠄾󠅟󠅤󠄐󠄼󠅟󠅗󠅙󠅞󠄬󠅒󠅢󠄟󠄮󠇘󠆭󠆘󠇙󠆝󠅵󠇗󠆭󠆁󠄐󠇗󠅹󠅸󠇖󠆍󠅳󠇖󠅹󠅰󠇖󠆌󠅹󠄬󠅒󠅢󠄟󠄮
(4)自密实混凝土和混凝土底座采用限位凹槽的方式进行限位,每块轨道板下设两个凹槽,凹槽尺寸为1000mm×700mm×100mm(长×宽×深),两凹槽中心间距为3.6m。限位凹槽周围设置弹性垫层。自密实混凝土和混凝土底座之间设置4mm厚的隔离层(土工布)。󠄐󠄹󠅀󠄪󠄣󠄞󠄡󠄤󠄡󠄞󠄤󠄠󠄞󠄢󠄤󠄢󠄬󠅒󠅢󠄟󠄮󠄐󠅅󠄹󠄴󠄪󠄾󠅟󠅤󠄐󠄼󠅟󠅗󠅙󠅞󠄬󠅒󠅢󠄟󠄮󠇘󠆭󠆘󠇙󠆝󠅵󠇗󠆭󠆁󠄐󠇗󠅹󠅸󠇖󠆍󠅳󠇖󠅹󠅰󠇖󠆌󠅹󠄬󠅒󠅢󠄟󠄮
(5)底座顶面及限位凹槽底面铺设橡胶隔振垫,厚度为27mm,刚度为0.03N/mm2,减振效果为-8dB。减振区段两端分别设长81m的过渡段(分为三级过渡,每级长约27m,通过5块板实现)。󠄐󠄹󠅀󠄪󠄣󠄞󠄡󠄤󠄡󠄞󠄤󠄠󠄞󠄢󠄤󠄢󠄬󠅒󠅢󠄟󠄮󠄐󠅅󠄹󠄴󠄪󠄾󠅟󠅤󠄐󠄼󠅟󠅗󠅙󠅞󠄬󠅒󠅢󠄟󠄮󠇘󠆭󠆘󠇙󠆝󠅵󠇗󠆭󠆁󠄐󠇗󠅹󠅸󠇖󠆍󠅳󠇖󠅹󠅰󠇖󠆌󠅹󠄬󠅒󠅢󠄟󠄮
(6)混凝土底座在现场浇筑并分段设置,于每2块轨道板对应长度设置宽度为20mm的伸缩缝(充填材料为聚乙烯泡沫塑料板),并在伸缩缝顶面及两侧用有机硅酮填缝。󠄐󠄹󠅀󠄪󠄣󠄞󠄡󠄤󠄡󠄞󠄤󠄠󠄞󠄢󠄤󠄢󠄬󠅒󠅢󠄟󠄮󠄐󠅅󠄹󠄴󠄪󠄾󠅟󠅤󠄐󠄼󠅟󠅗󠅙󠅞󠄬󠅒󠅢󠄟󠄮󠇘󠆭󠆘󠇙󠆝󠅵󠇗󠆭󠆁󠄐󠇗󠅹󠅸󠇖󠆍󠅳󠇖󠅹󠅰󠇖󠆌󠅹󠄬󠅒󠅢󠄟󠄮
(7)曲线超高在混凝土底座上实现,采取降低内轨、抬高外轨的方式。󠄐󠄹󠅀󠄪󠄣󠄞󠄡󠄤󠄡󠄞󠄤󠄠󠄞󠄢󠄤󠄢󠄬󠅒󠅢󠄟󠄮󠄐󠅅󠄹󠄴󠄪󠄾󠅟󠅤󠄐󠄼󠅟󠅗󠅙󠅞󠄬󠅒󠅢󠄟󠄮󠇘󠆭󠆘󠇙󠆝󠅵󠇗󠆭󠆁󠄐󠇗󠅹󠅸󠇖󠆍󠅳󠇖󠅹󠅰󠇖󠆌󠅹󠄬󠅒󠅢󠄟󠄮
4 施工流程
对于地下线普通型预制板整体道床,可将自密实混凝土与底座施工合二为一,即在测量放样后直接绑扎自密实混凝土底座钢筋并设置限位凹槽;而对于路基段普通型预制板整体道床,则需要将底座和自密实混凝土分开施工。
地下线减振垫浮置板道床(预制板式)的施工流程与路基段普通型预制板整体道床大体相同,只是在底座及凹槽施工和自密实混凝土钢筋绑扎之间增加了橡胶隔振垫安装的步骤。󠄐󠄹󠅀󠄪󠄣󠄞󠄡󠄤󠄡󠄞󠄤󠄠󠄞󠄢󠄤󠄢󠄬󠅒󠅢󠄟󠄮󠄐󠅅󠄹󠄴󠄪󠄾󠅟󠅤󠄐󠄼󠅟󠅗󠅙󠅞󠄬󠅒󠅢󠄟󠄮󠇘󠆭󠆘󠇙󠆝󠅵󠇗󠆭󠆁󠄐󠇗󠅹󠅸󠇖󠆍󠅳󠇖󠅹󠅰󠇖󠆌󠅹󠄬󠅒󠅢󠄟󠄮
三种预制板整体道床的施工流程见图5。󠄐󠄹󠅀󠄪󠄣󠄞󠄡󠄤󠄡󠄞󠄤󠄠󠄞󠄢󠄤󠄢󠄬󠅒󠅢󠄟󠄮󠄐󠅅󠄹󠄴󠄪󠄾󠅟󠅤󠄐󠄼󠅟󠅗󠅙󠅞󠄬󠅒󠅢󠄟󠄮󠇘󠆭󠆘󠇙󠆝󠅵󠇗󠆭󠆁󠄐󠇗󠅹󠅸󠇖󠆍󠅳󠇖󠅹󠅰󠇖󠆌󠅹󠄬󠅒󠅢󠄟󠄮

图5 三种预制板整体道床施工流程
5 施工工艺
5.1 预应力轨道板
预制轨道板(及板下限位凸台)在工厂预制,采用双向先张预应力体系,以“矩阵单元法”的方式生产。
单块预制轨道板的尺寸为5300mm×2500mm×200mm(长×宽×高),板下限位凸台的尺寸为700mm×400mm×100mm(长×宽×高)。󠄐󠄹󠅀󠄪󠄣󠄞󠄡󠄤󠄡󠄞󠄤󠄠󠄞󠄢󠄤󠄢󠄬󠅒󠅢󠄟󠄮󠄐󠅅󠄹󠄴󠄪󠄾󠅟󠅤󠄐󠄼󠅟󠅗󠅙󠅞󠄬󠅒󠅢󠄟󠄮󠇘󠆭󠆘󠇙󠆝󠅵󠇗󠆭󠆁󠄐󠇗󠅹󠅸󠇖󠆍󠅳󠇖󠅹󠅰󠇖󠆌󠅹󠄬󠅒󠅢󠄟󠄮
5.2 底座及凹槽施工
底座及凹槽的施工流程为:基底植筋→CPⅢ测量放样→安装钢筋网片→安装底座及凹槽模板→浇筑底座混凝土→混凝土养护→伸缩缝填筑。
(1)基底处理
在预制板整体道床范围内,隧道底板上需要植入锚固深度为110mm的YG2型M16×245膨胀螺栓,道床内钢筋应与露出结构底板的膨胀螺栓绑扎,沿线路方向按1.2m/6个进行设置(沿线路中线对称布置)。󠄐󠄹󠅀󠄪󠄣󠄞󠄡󠄤󠄡󠄞󠄤󠄠󠄞󠄢󠄤󠄢󠄬󠅒󠅢󠄟󠄮󠄐󠅅󠄹󠄴󠄪󠄾󠅟󠅤󠄐󠄼󠅟󠅗󠅙󠅞󠄬󠅒󠅢󠄟󠄮󠇘󠆭󠆘󠇙󠆝󠅵󠇗󠆭󠆁󠄐󠇗󠅹󠅸󠇖󠆍󠅳󠇖󠅹󠅰󠇖󠆌󠅹󠄬󠅒󠅢󠄟󠄮
(2)底座及限位凹槽施工
底座基础钢筋为CRB550级冷轧钢筋,也可采用HRB400级热轧螺纹钢筋(现场焊接)。应在焊接网下部网片处放置保护层垫块(最低数量为4个/m2),并确保保护层厚度满足相关设计要求[5]。在曲线超高及缓和曲线地段,应针对超高值相应调整两侧的构造及立筋尺寸。󠄐󠄹󠅀󠄪󠄣󠄞󠄡󠄤󠄡󠄞󠄤󠄠󠄞󠄢󠄤󠄢󠄬󠅒󠅢󠄟󠄮󠄐󠅅󠄹󠄴󠄪󠄾󠅟󠅤󠄐󠄼󠅟󠅗󠅙󠅞󠄬󠅒󠅢󠄟󠄮󠇘󠆭󠆘󠇙󠆝󠅵󠇗󠆭󠆁󠄐󠇗󠅹󠅸󠇖󠆍󠅳󠇖󠅹󠅰󠇖󠆌󠅹󠄬󠅒󠅢󠄟󠄮
(3)底座混凝土浇筑
在完成模板及全部所需钢筋的安装后(底座混凝土浇筑之前),需对其几何尺寸及高程进行检查。浇筑时,应注意限位凹槽处不得有过振或漏振等现象发生。在浇筑过程中,应重点控制混凝土面的高程及平整度。在混凝土强度达到5MPa后,方可拆除模具;底座混凝土应分区连续浇筑,不得出现中断。󠄐󠄹󠅀󠄪󠄣󠄞󠄡󠄤󠄡󠄞󠄤󠄠󠄞󠄢󠄤󠄢󠄬󠅒󠅢󠄟󠄮󠄐󠅅󠄹󠄴󠄪󠄾󠅟󠅤󠄐󠄼󠅟󠅗󠅙󠅞󠄬󠅒󠅢󠄟󠄮󠇘󠆭󠆘󠇙󠆝󠅵󠇗󠆭󠆁󠄐󠇗󠅹󠅸󠇖󠆍󠅳󠇖󠅹󠅰󠇖󠆌󠅹󠄬󠅒󠅢󠄟󠄮
(4)伸缩缝填筑
嵌缝材料为聚苯乙烯,伸缩缝顶面和两侧填充材料为有机硅酮[6]。底座板伸缩缝的缝槽应保持干燥、洁净,其表面应平整、连续,无起皮、剥落现象。聚苯乙烯泡沫塑料应牢固地粘合在缝壁上,嵌填密实且没有气泡。󠄐󠄹󠅀󠄪󠄣󠄞󠄡󠄤󠄡󠄞󠄤󠄠󠄞󠄢󠄤󠄢󠄬󠅒󠅢󠄟󠄮󠄐󠅅󠄹󠄴󠄪󠄾󠅟󠅤󠄐󠄼󠅟󠅗󠅙󠅞󠄬󠅒󠅢󠄟󠄮󠇘󠆭󠆘󠇙󠆝󠅵󠇗󠆭󠆁󠄐󠇗󠅹󠅸󠇖󠆍󠅳󠇖󠅹󠅰󠇖󠆌󠅹󠄬󠅒󠅢󠄟󠄮
(5)橡胶隔振垫铺设
在底座板顶面及限位凹槽底面铺设橡胶隔振垫,厚度为27mm,刚度为0.03N/mm2。减振区段两端分别设长81m的过渡段(分为三级过渡,每级长约27m;由内到外,每级刚度为0.06N/mm2、0.09N/mm2、0.12N/mm2)。󠄐󠄹󠅀󠄪󠄣󠄞󠄡󠄤󠄡󠄞󠄤󠄠󠄞󠄢󠄤󠄢󠄬󠅒󠅢󠄟󠄮󠄐󠅅󠄹󠄴󠄪󠄾󠅟󠅤󠄐󠄼󠅟󠅗󠅙󠅞󠄬󠅒󠅢󠄟󠄮󠇘󠆭󠆘󠇙󠆝󠅵󠇗󠆭󠆁󠄐󠇗󠅹󠅸󠇖󠆍󠅳󠇖󠅹󠅰󠇖󠆌󠅹󠄬󠅒󠅢󠄟󠄮
5.3 轨道板安装
(1)自密实混凝土钢筋绑扎
在安装轨道板之前,需要对自密实混凝土层的钢筋网进行绑扎与置放,并设置保护层垫块(确保保护层厚度满足设计要求)。为了使纵向钢筋在轨道板门型筋内侧处固定,需采用绝缘卡。󠄐󠄹󠅀󠄪󠄣󠄞󠄡󠄤󠄡󠄞󠄤󠄠󠄞󠄢󠄤󠄢󠄬󠅒󠅢󠄟󠄮󠄐󠅅󠄹󠄴󠄪󠄾󠅟󠅤󠄐󠄼󠅟󠅗󠅙󠅞󠄬󠅒󠅢󠄟󠄮󠇘󠆭󠆘󠇙󠆝󠅵󠇗󠆭󠆁󠄐󠇗󠅹󠅸󠇖󠆍󠅳󠇖󠅹󠅰󠇖󠆌󠅹󠄬󠅒󠅢󠄟󠄮
对于地下线普通型预制板整体道床,在其曲线超高及缓和曲线地段,应针对每个超高值相应调整两侧的构造及立筋尺寸,并设置限位凹槽,配筋亦需架设在限位凹槽处。󠄐󠄹󠅀󠄪󠄣󠄞󠄡󠄤󠄡󠄞󠄤󠄠󠄞󠄢󠄤󠄢󠄬󠅒󠅢󠄟󠄮󠄐󠅅󠄹󠄴󠄪󠄾󠅟󠅤󠄐󠄼󠅟󠅗󠅙󠅞󠄬󠅒󠅢󠄟󠄮󠇘󠆭󠆘󠇙󠆝󠅵󠇗󠆭󠆁󠄐󠇗󠅹󠅸󠇖󠆍󠅳󠇖󠅹󠅰󠇖󠆌󠅹󠄬󠅒󠅢󠄟󠄮
(2)铺前准备
根据施工的需要,将轨道板预先运输至铺轨基地。在装卸车时,需考虑轨道板的铺设顺序,避免后续铺设时出现二次倒板。轨道板应平整有序地堆放,并以方木支垫[7]。󠄐󠄹󠅀󠄪󠄣󠄞󠄡󠄤󠄡󠄞󠄤󠄠󠄞󠄢󠄤󠄢󠄬󠅒󠅢󠄟󠄮󠄐󠅅󠄹󠄴󠄪󠄾󠅟󠅤󠄐󠄼󠅟󠅗󠅙󠅞󠄬󠅒󠅢󠄟󠄮󠇘󠆭󠆘󠇙󠆝󠅵󠇗󠆭󠆁󠄐󠇗󠅹󠅸󠇖󠆍󠅳󠇖󠅹󠅰󠇖󠆌󠅹󠄬󠅒󠅢󠄟󠄮
轨道板运输到位后,需要对底座板及隔离层表面进行清理。粗铺前需精确放线,保证粗铺时轨道板中心线与线路中心线的偏差不大于10mm。此时,需要预先将支撑垫木放置在底座表面上,其位置为轨道板两侧端头处。󠄐󠄹󠅀󠄪󠄣󠄞󠄡󠄤󠄡󠄞󠄤󠄠󠄞󠄢󠄤󠄢󠄬󠅒󠅢󠄟󠄮󠄐󠅅󠄹󠄴󠄪󠄾󠅟󠅤󠄐󠄼󠅟󠅗󠅙󠅞󠄬󠅒󠅢󠄟󠄮󠇘󠆭󠆘󠇙󠆝󠅵󠇗󠆭󠆁󠄐󠇗󠅹󠅸󠇖󠆍󠅳󠇖󠅹󠅰󠇖󠆌󠅹󠄬󠅒󠅢󠄟󠄮
(3)轨道板粗铺
在铺轨机的运作下,将轨道板吊运至铺设位置,再通过人工及粗铺专用设备进行初步调整,使轨道板的横向偏差不大于5mm,纵向偏差不大于10mm,高程偏差不大于5mm。粗铺时,应注意轨道板的放置方向,即轨道板接地端子应位于线路外侧。完成粗铺调整后,将精调设备安装于轨道板预埋套筒处,撤出支撑垫木,再对轨道板进行精调。󠄐󠄹󠅀󠄪󠄣󠄞󠄡󠄤󠄡󠄞󠄤󠄠󠄞󠄢󠄤󠄢󠄬󠅒󠅢󠄟󠄮󠄐󠅅󠄹󠄴󠄪󠄾󠅟󠅤󠄐󠄼󠅟󠅗󠅙󠅞󠄬󠅒󠅢󠄟󠄮󠇘󠆭󠆘󠇙󠆝󠅵󠇗󠆭󠆁󠄐󠇗󠅹󠅸󠇖󠆍󠅳󠇖󠅹󠅰󠇖󠆌󠅹󠄬󠅒󠅢󠄟󠄮
在新机场线的施工中,引进了自适应轮胎式铺轨机和混凝土罐车的配合施工,平均铺设能力可达到70~80m/d;新设备的使用降低了混凝土的倒运频率,提高了施工效率。󠄐󠄹󠅀󠄪󠄣󠄞󠄡󠄤󠄡󠄞󠄤󠄠󠄞󠄢󠄤󠄢󠄬󠅒󠅢󠄟󠄮󠄐󠅅󠄹󠄴󠄪󠄾󠅟󠅤󠄐󠄼󠅟󠅗󠅙󠅞󠄬󠅒󠅢󠄟󠄮󠇘󠆭󠆘󠇙󠆝󠅵󠇗󠆭󠆁󠄐󠇗󠅹󠅸󠇖󠆍󠅳󠇖󠅹󠅰󠇖󠆌󠅹󠄬󠅒󠅢󠄟󠄮
5.4 轨道板精调
轨道板精调的流程为:输入设计值数据→架设全站仪并校准→安放棱镜架→精调固定[8]。后续需对数据进行记录和复核。
在新机场线的施工中,采用3D精调器和LeicaTS30快速精调系统对轨道板进行精调。精调开始前,需要对粗铺结果进行检查。精调过程中,要特别注意过渡段的搭接,确保线形平顺。󠄐󠄹󠅀󠄪󠄣󠄞󠄡󠄤󠄡󠄞󠄤󠄠󠄞󠄢󠄤󠄢󠄬󠅒󠅢󠄟󠄮󠄐󠅅󠄹󠄴󠄪󠄾󠅟󠅤󠄐󠄼󠅟󠅗󠅙󠅞󠄬󠅒󠅢󠄟󠄮󠇘󠆭󠆘󠇙󠆝󠅵󠇗󠆭󠆁󠄐󠇗󠅹󠅸󠇖󠆍󠅳󠇖󠅹󠅰󠇖󠆌󠅹󠄬󠅒󠅢󠄟󠄮
精调完成后,需对已完成精调的轨道板进行防护,并设置跨线通道,防范对轨道板的踩踏或撞击等行为。󠄐󠄹󠅀󠄪󠄣󠄞󠄡󠄤󠄡󠄞󠄤󠄠󠄞󠄢󠄤󠄢󠄬󠅒󠅢󠄟󠄮󠄐󠅅󠄹󠄴󠄪󠄾󠅟󠅤󠄐󠄼󠅟󠅗󠅙󠅞󠄬󠅒󠅢󠄟󠄮󠇘󠆭󠆘󠇙󠆝󠅵󠇗󠆭󠆁󠄐󠇗󠅹󠅸󠇖󠆍󠅳󠇖󠅹󠅰󠇖󠆌󠅹󠄬󠅒󠅢󠄟󠄮
如果环境产生较大温差变化或放置时间较久,则有必要进行二次调校。󠄐󠄹󠅀󠄪󠄣󠄞󠄡󠄤󠄡󠄞󠄤󠄠󠄞󠄢󠄤󠄢󠄬󠅒󠅢󠄟󠄮󠄐󠅅󠄹󠄴󠄪󠄾󠅟󠅤󠄐󠄼󠅟󠅗󠅙󠅞󠄬󠅒󠅢󠄟󠄮󠇘󠆭󠆘󠇙󠆝󠅵󠇗󠆭󠆁󠄐󠇗󠅹󠅸󠇖󠆍󠅳󠇖󠅹󠅰󠇖󠆌󠅹󠄬󠅒󠅢󠄟󠄮
5.5 自密实混凝土灌注
(1)模板支护
首先应清理轨道板下的灰尘及其他杂物,依照规定进行侧面模板和端头模板的支设。模板应设置排气孔道,采用弹性密封条密封侧面模板和端头模板。模板安装完成后,应满足以下要求:灌注过程中无漏浆现象,拆模后无“烂根”现象。󠄐󠄹󠅀󠄪󠄣󠄞󠄡󠄤󠄡󠄞󠄤󠄠󠄞󠄢󠄤󠄢󠄬󠅒󠅢󠄟󠄮󠄐󠅅󠄹󠄴󠄪󠄾󠅟󠅤󠄐󠄼󠅟󠅗󠅙󠅞󠄬󠅒󠅢󠄟󠄮󠇘󠆭󠆘󠇙󠆝󠅵󠇗󠆭󠆁󠄐󠇗󠅹󠅸󠇖󠆍󠅳󠇖󠅹󠅰󠇖󠆌󠅹󠄬󠅒󠅢󠄟󠄮
(2)灌注
应确保底座顶面及隔离层上无积水、灰尘、污垢等;轨道板应以薄膜覆盖,避免轨道板在灌注过程中受到污染。同时对底座施工质量、轨道板精调结果、自密实混凝土层厚度进行复测。应使用专门的压紧装置固定,并在曲线超高及缓和曲线地段配备防侧移固定装置。󠄐󠄹󠅀󠄪󠄣󠄞󠄡󠄤󠄡󠄞󠄤󠄠󠄞󠄢󠄤󠄢󠄬󠅒󠅢󠄟󠄮󠄐󠅅󠄹󠄴󠄪󠄾󠅟󠅤󠄐󠄼󠅟󠅗󠅙󠅞󠄬󠅒󠅢󠄟󠄮󠇘󠆭󠆘󠇙󠆝󠅵󠇗󠆭󠆁󠄐󠇗󠅹󠅸󠇖󠆍󠅳󠇖󠅹󠅰󠇖󠆌󠅹󠄬󠅒󠅢󠄟󠄮
灌注前,须先制作混凝土试样(至少3组),并测定温度、坍落度、含气量、泌水率等相关参数,符合相关施工规范后方可灌注。󠄐󠄹󠅀󠄪󠄣󠄞󠄡󠄤󠄡󠄞󠄤󠄠󠄞󠄢󠄤󠄢󠄬󠅒󠅢󠄟󠄮󠄐󠅅󠄹󠄴󠄪󠄾󠅟󠅤󠄐󠄼󠅟󠅗󠅙󠅞󠄬󠅒󠅢󠄟󠄮󠇘󠆭󠆘󠇙󠆝󠅵󠇗󠆭󠆁󠄐󠇗󠅹󠅸󠇖󠆍󠅳󠇖󠅹󠅰󠇖󠆌󠅹󠄬󠅒󠅢󠄟󠄮
灌注过程中,应安排专门的工程师实时监查,采用持续缓慢搅拌的方式注入,以免引发假凝从而丧失流动性。当注入量接近一半时,注入速度应进一步降低。可通过轨道板2个观察孔及模板四角排气孔观察板下的自密实混凝土流动情况,当自密实混凝土浆面全部越过轨道板面时,应及时关闭灌注料斗阀门。󠄐󠄹󠅀󠄪󠄣󠄞󠄡󠄤󠄡󠄞󠄤󠄠󠄞󠄢󠄤󠄢󠄬󠅒󠅢󠄟󠄮󠄐󠅅󠄹󠄴󠄪󠄾󠅟󠅤󠄐󠄼󠅟󠅗󠅙󠅞󠄬󠅒󠅢󠄟󠄮󠇘󠆭󠆘󠇙󠆝󠅵󠇗󠆭󠆁󠄐󠇗󠅹󠅸󠇖󠆍󠅳󠇖󠅹󠅰󠇖󠆌󠅹󠄬󠅒󠅢󠄟󠄮
自密实混凝土的搅拌时间不宜超过150min。灌注单块轨道板混凝土的过程应连续进行(单块灌注时间宜为6~12min)。󠄐󠄹󠅀󠄪󠄣󠄞󠄡󠄤󠄡󠄞󠄤󠄠󠄞󠄢󠄤󠄢󠄬󠅒󠅢󠄟󠄮󠄐󠅅󠄹󠄴󠄪󠄾󠅟󠅤󠄐󠄼󠅟󠅗󠅙󠅞󠄬󠅒󠅢󠄟󠄮󠇘󠆭󠆘󠇙󠆝󠅵󠇗󠆭󠆁󠄐󠇗󠅹󠅸󠇖󠆍󠅳󠇖󠅹󠅰󠇖󠆌󠅹󠄬󠅒󠅢󠄟󠄮
灌注完成后,应再次确认起立位置,将灌注口和四角排气孔处的多余混凝土清除掉,并检查混凝土有无漏出现象,并及时紧密覆盖住混凝土的暴露面(用篷布、塑料布等),防止表面水分蒸发。󠄐󠄹󠅀󠄪󠄣󠄞󠄡󠄤󠄡󠄞󠄤󠄠󠄞󠄢󠄤󠄢󠄬󠅒󠅢󠄟󠄮󠄐󠅅󠄹󠄴󠄪󠄾󠅟󠅤󠄐󠄼󠅟󠅗󠅙󠅞󠄬󠅒󠅢󠄟󠄮󠇘󠆭󠆘󠇙󠆝󠅵󠇗󠆭󠆁󠄐󠇗󠅹󠅸󠇖󠆍󠅳󠇖󠅹󠅰󠇖󠆌󠅹󠄬󠅒󠅢󠄟󠄮
(3)养护与拆模
待自密实混凝土初凝完成后,应及时涂刷养护液并进行覆盖养护(14d是最低的养护时间)。当自密实混凝土强度达到10MPa且拆模行为不会导致表面及棱角受损时,方可将3D精调器、压紧装置及四周模板拆除。拆模按立模的相反顺序进行,当模板与自密实混凝土脱离后,方可将模板完全拆卸。󠄐󠄹󠅀󠄪󠄣󠄞󠄡󠄤󠄡󠄞󠄤󠄠󠄞󠄢󠄤󠄢󠄬󠅒󠅢󠄟󠄮󠄐󠅅󠄹󠄴󠄪󠄾󠅟󠅤󠄐󠄼󠅟󠅗󠅙󠅞󠄬󠅒󠅢󠄟󠄮󠇘󠆭󠆘󠇙󠆝󠅵󠇗󠆭󠆁󠄐󠇗󠅹󠅸󠇖󠆍󠅳󠇖󠅹󠅰󠇖󠆌󠅹󠄬󠅒󠅢󠄟󠄮
拆模之后,待自密实混凝土强度值达到设计值后,轨道板方可承受全部设计荷载。此时,结束对自密实混凝土的养护。󠄐󠄹󠅀󠄪󠄣󠄞󠄡󠄤󠄡󠄞󠄤󠄠󠄞󠄢󠄤󠄢󠄬󠅒󠅢󠄟󠄮󠄐󠅅󠄹󠄴󠄪󠄾󠅟󠅤󠄐󠄼󠅟󠅗󠅙󠅞󠄬󠅒󠅢󠄟󠄮󠇘󠆭󠆘󠇙󠆝󠅵󠇗󠆭󠆁󠄐󠇗󠅹󠅸󠇖󠆍󠅳󠇖󠅹󠅰󠇖󠆌󠅹󠄬󠅒󠅢󠄟󠄮
6 结束语
新机场线是中国第一条设计速度达160km/h的地铁线,被誉为“北京市轨道交通建设的里程碑”并于2019年9月底正式开通运营。该线拥有稳定、良好的轨道结构,快速、平稳的行驶状态,安全、先进的运行水平,是对地下线普通型预制板整体道床、路基段普通型预制板整体道床和地下线减振垫浮置板道床设计和施工的充分肯定。
文章来源:
原文名称:时速160km城市轨道交通预制板整体道床设计与施工󠄐󠄹󠅀󠄪󠄣󠄞󠄡󠄤󠄡󠄞󠄤󠄠󠄞󠄢󠄤󠄢󠄬󠅒󠅢󠄟󠄮󠄐󠅅󠄹󠄴󠄪󠄾󠅟󠅤󠄐󠄼󠅟󠅗󠅙󠅞󠄬󠅒󠅢󠄟󠄮󠇘󠆭󠆘󠇙󠆝󠅵󠇗󠆭󠆁󠄐󠇗󠅹󠅸󠇖󠆍󠅳󠇖󠅹󠅰󠇖󠆌󠅹󠄬󠅒󠅢󠄟󠄮
作者信息:张睿(中铁工程设计咨询集团有限公司,北京 100055)󠄐󠄹󠅀󠄪󠄣󠄞󠄡󠄤󠄡󠄞󠄤󠄠󠄞󠄢󠄤󠄢󠄬󠅒󠅢󠄟󠄮󠄐󠅅󠄹󠄴󠄪󠄾󠅟󠅤󠄐󠄼󠅟󠅗󠅙󠅞󠄬󠅒󠅢󠄟󠄮󠇘󠆭󠆘󠇙󠆝󠅵󠇗󠆭󠆁󠄐󠇗󠅹󠅸󠇖󠆍󠅳󠇖󠅹󠅰󠇖󠆌󠅹󠄬󠅒󠅢󠄟󠄮
期刊信息:铁道勘察 2020年第3期󠄐󠄹󠅀󠄪󠄣󠄞󠄡󠄤󠄡󠄞󠄤󠄠󠄞󠄢󠄤󠄢󠄬󠅒󠅢󠄟󠄮󠄐󠅅󠄹󠄴󠄪󠄾󠅟󠅤󠄐󠄼󠅟󠅗󠅙󠅞󠄬󠅒󠅢󠄟󠄮󠇘󠆭󠆘󠇙󠆝󠅵󠇗󠆭󠆁󠄐󠇗󠅹󠅸󠇖󠆍󠅳󠇖󠅹󠅰󠇖󠆌󠅹󠄬󠅒󠅢󠄟󠄮