钢轨打磨技术起源于20世纪50年代,经过60多年的发展已经成为高速和重载铁路一项重要的钢轨修理技术,并得到了普遍的应用。钢轨打磨技术可有效治理和控制钢轨表面病害,延长钢轨的使用寿命。我国铁路于20世纪80年代引进钢轨打磨技术,并逐渐成为我国铁路一项基本的轨道维护技术。目前大部分铁路局已配备了48磨头和96磨头的大型钢轨打磨车。长期以来,我国铁路的钢轨打磨以修理性打磨为主,即以磨削钢轨顶部的波磨和剥离掉块为主、以去除钢轨的塑性流变(辗边)为辅。近年来随着我国高速铁路的快速发展,钢轨预打磨越来越受到重视,并已成为高速铁路正式运营前的一项必不可少的工序。本文从钢轨的预打磨廓面设计、钢轨打磨周期和打磨参数方面重点论述高速铁路的钢轨打磨技术。󠄐󠄹󠅀󠄪󠄡󠄨󠄞󠄡󠄨󠄨󠄞󠄡󠄦󠄣󠄞󠄢󠄣󠄦󠄬󠅒󠅢󠄟󠄮󠄐󠅅󠄹󠄴󠄪󠄾󠅟󠅤󠄐󠄼󠅟󠅗󠅙󠅞󠄬󠅒󠅢󠄟󠄮󠇘󠆭󠆘󠇙󠆝󠅵󠇗󠆭󠆁󠄐󠇗󠅹󠅸󠇖󠆍󠅳󠇖󠅹󠅰󠇖󠆌󠅹󠄬󠅒󠅢󠄟󠄮
1 钢轨预打磨廓面设计
1.1 轮轨接触区域分析
钢轨预打磨是对铺设上道后的新钢轨进行打磨,其目的除了要打磨掉钢轨表面的脱碳层以及缺陷和伤损、提高轨道的平顺性(包括使钢轨焊接接头平直度与钢轨母材平直度基本一致)外,还要形成与车轮型面相匹配的轨头廓面,使轮轨接触主要发生在轨头踏面中央区域。这是有效改善轮轨接触状态的方法之一,也是我国高速铁路钢轨预打磨不同于国外的特点之一。轮轨接触区域的划分如图1所示。
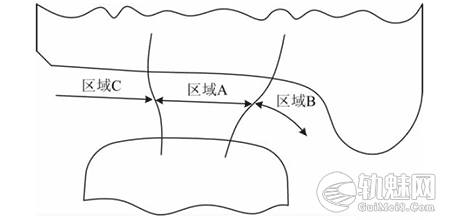
图1 轮轨接触区域划分示意图
由图1可知,高速动车组在直线和大半经曲线线路上运行时,轮轨在区域A 接触时能够使轮轨接触应力以及横向蠕滑率和蠕滑力最小。轮轨在区域B接触时又有两点接触、单点接触和共形接触3种形式(见图2);当轮轨在区域B接触时,最好能够形成共形接触。轮轨在区域A 接触和在区域B形成共形接触是轮轨匹配的理想状态,也是车轮型面和轨头廓面设计所追求的目标。
1.2 钢轨预打磨轨头廓面设计
日本铁路和法国铁路由于在车轮型面和轨头廓面的设计中考虑了轨底坡、轮背内侧距等轮轨几何参数,因此按轨头的原始廓面进行钢轨打磨后,钢轨的走行光带处于轨头踏面的中央区域,使得轮轨匹配状态较为理想。德国高速铁路针对1∶40轨底坡存在的轮轨不匹配问题,通过优化轨头廓面,研发出了60E2型钢轨。此后,无论是对之前铺设的60E1型钢轨还是之后铺设的60E2型钢轨,均按60E2型钢轨的轨头廓面对钢轨进行预打磨。
我国高速铁路采用LMA(CRH1和CRH2动车组)、S1002G(CRH3动车组)和XP55(CRH5动车组)3种车轮型面。其中按照1:20轨底坡和1360mm轮背内侧距设计的S1002G和XP55车轮型面用在我国高速铁路1:40轨底坡和1353mm轮背内侧距的条件下时,一方面将造成轮轨接触点偏向于轨距角,有可能发生两点接触;另一方面,不仅加大了轮轨游间,同时车轮的名义滚动圆半径也发生改变;这些因素均对轮轨匹配关系产生不利影响。但改变轨底坡和轮背内侧距又不太可能,因此只能从钢轨预打磨轨头廓面寻求解决方案。若按我国钢轨原始轨头廓面(60kg/m-1钢轨轨头廓面)进行钢轨预打磨,必然造成轮轨接触点偏向轨距角侧,甚至出现2条走行光带的情况,这已被石太、京津和武广客运专线钢轨预打磨后的实际轮轨走行光带所证明,同时也表明我国铁路采用的钢轨原始轨头廓面与车轮型面不匹配。因此按车轮的型面设计钢轨的预打磨轨头廓面并据此进行钢轨预打磨,是改善轮轨匹配状态行之有效的途径。
根据车轮型面设计钢轨的预打磨轨头廓面,并按此廓面对钢轨打磨,可使轮轨在区域A 接触或在区域B形成共形接触。由此得出适用于不同车轮型面的钢轨预打磨深度理论设计值,见表1。󠄐󠄹󠅀󠄪󠄡󠄨󠄞󠄡󠄨󠄨󠄞󠄡󠄦󠄣󠄞󠄢󠄣󠄦󠄬󠅒󠅢󠄟󠄮󠄐󠅅󠄹󠄴󠄪󠄾󠅟󠅤󠄐󠄼󠅟󠅗󠅙󠅞󠄬󠅒󠅢󠄟󠄮󠇘󠆭󠆘󠇙󠆝󠅵󠇗󠆭󠆁󠄐󠇗󠅹󠅸󠇖󠆍󠅳󠇖󠅹󠅰󠇖󠆌󠅹󠄬󠅒󠅢󠄟󠄮
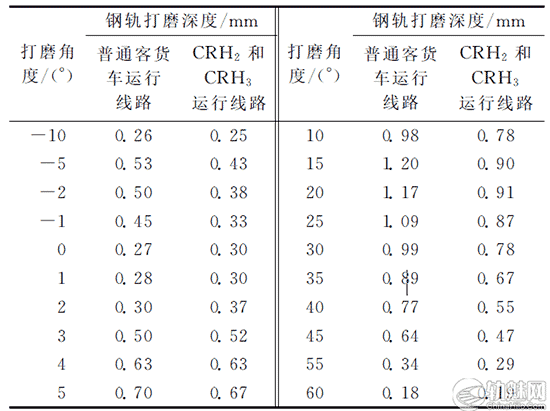
表1 钢轨打磨深度理论设计值
钢轨打磨角度与设计出的适用于LMA和S1002G车轮型面的钢轨预打磨轨头廓面(以下简称预打磨设计廓面)如图3所示;按预打磨设计廓面对钢轨预打磨后的轮轨接触关系如图4所示。图3中,虚线表示预打磨设计廓面。

图3 适用于LMA和S1002G车轮型面的预打磨设计廓面
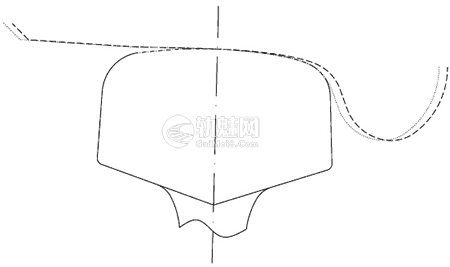
图4 按预打磨设计廓面对钢轨预打磨后的轮轨接触关系
分别按原始廓面和上述预打磨设计廓面进行钢轨预打磨,结果按原始廓面进行预打磨后的轮轨走行光带不理想,有的线路还出现了晃车现象,不得不在短时间内重新进行钢轨打磨;而按预打磨设计廓面对钢轨进行预打磨后,轮轨接触在轨头中央(轮轨走行光带居中),轮轨走行光带的宽度达20~30mm,表明按预打磨设计廓面对钢轨预打磨后能改善轮轨匹配状态。
为了使钢轨预打磨后打磨廓面达到设计要求,可以采用特制的样板或廓面测量仪对轨头廓面进行检测。钢轨预打磨后的实际轨头廓面与预打磨设计廓面的误差在轨距角部位应控制在-0.1~0.3mm以内。󠄐󠄹󠅀󠄪󠄡󠄨󠄞󠄡󠄨󠄨󠄞󠄡󠄦󠄣󠄞󠄢󠄣󠄦󠄬󠅒󠅢󠄟󠄮󠄐󠅅󠄹󠄴󠄪󠄾󠅟󠅤󠄐󠄼󠅟󠅗󠅙󠅞󠄬󠅒󠅢󠄟󠄮󠇘󠆭󠆘󠇙󠆝󠅵󠇗󠆭󠆁󠄐󠇗󠅹󠅸󠇖󠆍󠅳󠇖󠅹󠅰󠇖󠆌󠅹󠄬󠅒󠅢󠄟󠄮
2 钢轨打磨周期
高速铁路的钢轨打磨周期原则上应根据轨面状态(包括车轮走行光带、钢轨波磨、轨面伤损等)、钢轨轨面发生明显加工硬化的时间节点或通过总重确定。
2.1 国外高速铁路钢轨打磨周期
法国TGV高速铁路新线在开通前要进行1次钢轨预打磨;而开通后采用不定期打磨,具体何时打磨取决于轨检车检测和拍摄到的钢轨表面状态,打磨的目的主要是将因道砟飞溅而造成的轨面伤损打磨掉。一般打磨周期为3~4年。
日本铁路规定:高速铁路更换钢轨后1年内必须进行1次钢轨打磨,随后的钢轨打磨周期则与减少噪声有关。对于通过住宅密集区的线路是1年或每30Mt通过总重打磨1次钢轨,对于通过其他区域的线路,根据各区域的居民相对密度按通过总重30~60Mt不等确定钢轨打磨周期。可见,治理噪声是日本高速铁路进行钢轨打磨的主要目的之一。󠄐󠄹󠅀󠄪󠄡󠄨󠄞󠄡󠄨󠄨󠄞󠄡󠄦󠄣󠄞󠄢󠄣󠄦󠄬󠅒󠅢󠄟󠄮󠄐󠅅󠄹󠄴󠄪󠄾󠅟󠅤󠄐󠄼󠅟󠅗󠅙󠅞󠄬󠅒󠅢󠄟󠄮󠇘󠆭󠆘󠇙󠆝󠅵󠇗󠆭󠆁󠄐󠇗󠅹󠅸󠇖󠆍󠅳󠇖󠅹󠅰󠇖󠆌󠅹󠄬󠅒󠅢󠄟󠄮
德国高速铁路实行钢轨的预打磨;对客货混运铁路(如汉诺威—维尔茨堡、曼海姆—斯图加特,动车组最大轴重19.5t,货车最大轴重22.5t)钢轨的打磨周期为每4年1次。󠄐󠄹󠅀󠄪󠄡󠄨󠄞󠄡󠄨󠄨󠄞󠄡󠄦󠄣󠄞󠄢󠄣󠄦󠄬󠅒󠅢󠄟󠄮󠄐󠅅󠄹󠄴󠄪󠄾󠅟󠅤󠄐󠄼󠅟󠅗󠅙󠅞󠄬󠅒󠅢󠄟󠄮󠇘󠆭󠆘󠇙󠆝󠅵󠇗󠆭󠆁󠄐󠇗󠅹󠅸󠇖󠆍󠅳󠇖󠅹󠅰󠇖󠆌󠅹󠄬󠅒󠅢󠄟󠄮
2.2 我国高速铁路钢轨打磨周期
根据钢轨预打磨的作用,在轨道精调后至高铁正式开通运行前应进行并完成钢轨预打磨。京津、武广、郑西、京沪等250~350km/h-1速度等级的高速铁路以及石太、武合等200~250km/h-1速度等级的客运专线,在正式开通运营前均完成了钢轨的预打磨。
由于轴重轻,高速铁路的钢轨发生加工硬化的时间较长。根据京津城际铁路测量结果,该线路运营2年来通过总重约为30Mt,铺设的钢轨基本未出现明显的加工硬化。因此在确定高速铁路钢轨打磨周期时基本无需考虑疲劳问题,主要应考虑轨面状态以及噪声问题。󠄐󠄹󠅀󠄪󠄡󠄨󠄞󠄡󠄨󠄨󠄞󠄡󠄦󠄣󠄞󠄢󠄣󠄦󠄬󠅒󠅢󠄟󠄮󠄐󠅅󠄹󠄴󠄪󠄾󠅟󠅤󠄐󠄼󠅟󠅗󠅙󠅞󠄬󠅒󠅢󠄟󠄮󠇘󠆭󠆘󠇙󠆝󠅵󠇗󠆭󠆁󠄐󠇗󠅹󠅸󠇖󠆍󠅳󠇖󠅹󠅰󠇖󠆌󠅹󠄬󠅒󠅢󠄟󠄮
借鉴国外的经验,根据对京津城际铁路铺设钢轨的观测结果,建议我国高速铁路的钢轨打磨周期暂按每30~50Mt通过总重打磨1次确定,无砟轨道取上限,有砟轨道取下限。若钢轨预打磨未能达到预期效果,即车轮走行光带不居中、走行光带宽度变化较大甚至出现2条走行光带、或者车辆动力学响应超过限值时,应尽快安排打磨,以改善轮轨接触关系。󠄐󠄹󠅀󠄪󠄡󠄨󠄞󠄡󠄨󠄨󠄞󠄡󠄦󠄣󠄞󠄢󠄣󠄦󠄬󠅒󠅢󠄟󠄮󠄐󠅅󠄹󠄴󠄪󠄾󠅟󠅤󠄐󠄼󠅟󠅗󠅙󠅞󠄬󠅒󠅢󠄟󠄮󠇘󠆭󠆘󠇙󠆝󠅵󠇗󠆭󠆁󠄐󠇗󠅹󠅸󠇖󠆍󠅳󠇖󠅹󠅰󠇖󠆌󠅹󠄬󠅒󠅢󠄟󠄮
3 钢轨打磨参数
3.1 打磨深度
对钢轨进行预打磨,首先要保证消除高速铁路钢轨上的脱碳层。该脱碳层深度多数小于0.3mm,个别为0.3~0.5mm,其中硬度较低的全脱碳层深度约为0.1~0.2mm。因此,为了消除车轮走行面上硬度较低的全脱碳层,钢轨预打磨的深度在非工作边侧应大于0.2mm,在轮轨主要接触部位应于0.3mm。其次,为了使走行光带居中,根据具体的车轮型面,在轨距角部位的打磨深度应达到0.8~1.5mm。
在轨道施工中,工程车运行可能会造成轨面轧伤或擦伤。这些伤损也需要通过钢轨预打磨消除。当伤损深度在0.35~0.50mm 时,可使用小型平磨机打磨,并且打磨后的打磨面硬度应不高于钢轨原始硬度的50HB;当伤损深度超过0.5mm 时,应换轨或用铣磨车铣磨掉。󠄐󠄹󠅀󠄪󠄡󠄨󠄞󠄡󠄨󠄨󠄞󠄡󠄦󠄣󠄞󠄢󠄣󠄦󠄬󠅒󠅢󠄟󠄮󠄐󠅅󠄹󠄴󠄪󠄾󠅟󠅤󠄐󠄼󠅟󠅗󠅙󠅞󠄬󠅒󠅢󠄟󠄮󠇘󠆭󠆘󠇙󠆝󠅵󠇗󠆭󠆁󠄐󠇗󠅹󠅸󠇖󠆍󠅳󠇖󠅹󠅰󠇖󠆌󠅹󠄬󠅒󠅢󠄟󠄮
3.2 打磨小平面宽度
为保证钢轨打磨面连接的平顺性,同时避免一次进刀量过大而对钢轨造成伤损,需要对一次打磨形成的打磨小平面的宽度进行限制。轨头半径为13mm区域(约+15°~+60°)、半径为80mm区域(约+5°~+15°以及-5°~-15°)和半径为300mm区域(约-5°~+5°)打磨面的最大宽度分别为5,7和10mm (见图3)。打磨面沿钢轨纵向100mm长范围内的打磨面宽度最大变化量应不大于打磨面最大宽度的25%。
3.3 打磨面质量
钢轨打磨面的质量采用钢轨表面粗糙度、表面颜色和平直度来描述。
(1)表面粗糙度。
法国高速铁路规定,钢轨打磨后的钢轨表面粗糙度须小于5μm,英国铁路是小于7μm。参照欧洲标准,我国铁路规定钢轨打磨后的钢轨表面粗糙度应小于10μm。用96磨头的打磨车打磨2遍即可完成钢轨预打磨,并且钢轨表面粗糙度小于6μm。在打磨过程中应使用便携式粗糙度检测仪检测钢轨表面粗糙度。在10mm长范围之内的钢轨打磨面上,沿与钢轨打磨痕迹垂直方向至少测量6个点的钢轨表面粗糙度,而且这6个点的钢轨表面粗糙度须小于10μm。
(2)表面颜色。
用肉眼观测,钢轨打磨面应无连续的发蓝带。
(3)平直度。
用1m 测量尺(钢直尺或电子测量尺)测量钢轨母材和焊接接头轨顶面的平直度,应均不大于0.2mm/m-1。
3.4 打磨车作业速度和打磨遍数
钢轨打磨车的作业速度应根据其特性和打磨目的确定。48磨头打磨车的作业速度为8~12km/h-1,96磨头打磨车的作业速度,根据打磨车的不同功率而有所不同,一般为15~20km/h-1。长大坡道线路区段的钢轨打磨作业方向应为上坡方向,并严格控制打磨车的作业速度。
钢轨预打磨的打磨遍数:通常采用48磨头打磨车时为3~4遍,采用96磨头打磨车时为2遍。󠄐󠄹󠅀󠄪󠄡󠄨󠄞󠄡󠄨󠄨󠄞󠄡󠄦󠄣󠄞󠄢󠄣󠄦󠄬󠅒󠅢󠄟󠄮󠄐󠅅󠄹󠄴󠄪󠄾󠅟󠅤󠄐󠄼󠅟󠅗󠅙󠅞󠄬󠅒󠅢󠄟󠄮󠇘󠆭󠆘󠇙󠆝󠅵󠇗󠆭󠆁󠄐󠇗󠅹󠅸󠇖󠆍󠅳󠇖󠅹󠅰󠇖󠆌󠅹󠄬󠅒󠅢󠄟󠄮
4 轮轨走行光带的控制
[reply]
(1)钢轨打磨后,轮轨走行光带不宜太窄。虽然轮轨走行光带居中且较窄对减少晃车有利,但会加速车轮的凹磨,不利于延长车轮的镟修周期。对轨头半径为13mm 的部位多打磨,可使轮轨走行光带居中;对轨头半径为80mm 的部位少打磨,可使轮轨走行光带有较大的宽度。󠄐󠄹󠅀󠄪󠄡󠄨󠄞󠄡󠄨󠄨󠄞󠄡󠄦󠄣󠄞󠄢󠄣󠄦󠄬󠅒󠅢󠄟󠄮󠄐󠅅󠄹󠄴󠄪󠄾󠅟󠅤󠄐󠄼󠅟󠅗󠅙󠅞󠄬󠅒󠅢󠄟󠄮󠇘󠆭󠆘󠇙󠆝󠅵󠇗󠆭󠆁󠄐󠇗󠅹󠅸󠇖󠆍󠅳󠇖󠅹󠅰󠇖󠆌󠅹󠄬󠅒󠅢󠄟󠄮
(2)列车通过曲线线路时存在离心力,轮对会发生较大的横移,其外车轮轮缘易贴靠上股钢轨。因此在曲线线路对上股钢轨进行打磨时,轨距角的磨削量应大于直线线路钢轨轨距角的磨削量,否则曲线上股钢轨上的轮轨走行光带会偏向轨距角侧,甚至出现2条轮轨走行光带。󠄐󠄹󠅀󠄪󠄡󠄨󠄞󠄡󠄨󠄨󠄞󠄡󠄦󠄣󠄞󠄢󠄣󠄦󠄬󠅒󠅢󠄟󠄮󠄐󠅅󠄹󠄴󠄪󠄾󠅟󠅤󠄐󠄼󠅟󠅗󠅙󠅞󠄬󠅒󠅢󠄟󠄮󠇘󠆭󠆘󠇙󠆝󠅵󠇗󠆭󠆁󠄐󠇗󠅹󠅸󠇖󠆍󠅳󠇖󠅹󠅰󠇖󠆌󠅹󠄬󠅒󠅢󠄟󠄮
(3)在钢轨轧制过程中,钢轨轨冠饱满度会随着轧辊的磨损而发生变化,致使钢轨轨头廓面的实际形状与标准廓面之间存在差异。轨底坡在施工过程中也存在误差。因此,当采用相同的打磨程序对钢轨进行打磨时,如果出现不同的轮轨走行光带,应从钢轨轨冠饱满度和实际轨底坡误差的影响考虑,及时调整打磨程序,确保钢轨打磨后能使轮轨走行光带居中。󠄐󠄹󠅀󠄪󠄡󠄨󠄞󠄡󠄨󠄨󠄞󠄡󠄦󠄣󠄞󠄢󠄣󠄦󠄬󠅒󠅢󠄟󠄮󠄐󠅅󠄹󠄴󠄪󠄾󠅟󠅤󠄐󠄼󠅟󠅗󠅙󠅞󠄬󠅒󠅢󠄟󠄮󠇘󠆭󠆘󠇙󠆝󠅵󠇗󠆭󠆁󠄐󠇗󠅹󠅸󠇖󠆍󠅳󠇖󠅹󠅰󠇖󠆌󠅹󠄬󠅒󠅢󠄟󠄮
(4)钢轨打磨后要形成合理的打磨廓面,不能采用突出中间、磨削两边的方法使轮轨走行光带居中。󠄐󠄹󠅀󠄪󠄡󠄨󠄞󠄡󠄨󠄨󠄞󠄡󠄦󠄣󠄞󠄢󠄣󠄦󠄬󠅒󠅢󠄟󠄮󠄐󠅅󠄹󠄴󠄪󠄾󠅟󠅤󠄐󠄼󠅟󠅗󠅙󠅞󠄬󠅒󠅢󠄟󠄮󠇘󠆭󠆘󠇙󠆝󠅵󠇗󠆭󠆁󠄐󠇗󠅹󠅸󠇖󠆍󠅳󠇖󠅹󠅰󠇖󠆌󠅹󠄬󠅒󠅢󠄟󠄮
5 结 语
本文分析了3种轮轨接触区域对轮轨关系的影响,提出我国高速铁路钢轨预打磨廓面的设计应该与车轮的型面匹配,这是改善轮轨接触状态的一条行之有效的途径。给出了适用于不同车轮型面的钢轨预打磨深度理论设计值以及适用于LMA和S1002G车轮型面的钢轨预打磨轨头廓面。钢轨预打磨后的实际轨头廓面与预打磨设计廓面的误差在轨距角部位应控制在-0.1~0.3mm 以内。建议我国高速铁路的钢轨打磨周期暂按每30~50Mt通过总重打磨1次。关于60kg/m-1钢轨的预打磨深度,在轨距角部位应达到0.8~1.5mm,在主要轮轨接触部位应大于0.3mm。钢轨打磨后的表面粗糙度应小于10μm。采用48磨头打磨车时打磨3~4遍,采用96磨头打磨车时打磨2遍。
文章来源:
期刊:中国铁道科学 (2012年3月)󠄐󠄹󠅀󠄪󠄡󠄨󠄞󠄡󠄨󠄨󠄞󠄡󠄦󠄣󠄞󠄢󠄣󠄦󠄬󠅒󠅢󠄟󠄮󠄐󠅅󠄹󠄴󠄪󠄾󠅟󠅤󠄐󠄼󠅟󠅗󠅙󠅞󠄬󠅒󠅢󠄟󠄮󠇘󠆭󠆘󠇙󠆝󠅵󠇗󠆭󠆁󠄐󠇗󠅹󠅸󠇖󠆍󠅳󠇖󠅹󠅰󠇖󠆌󠅹󠄬󠅒󠅢󠄟󠄮
名称:高速铁路钢轨打磨关键技术研究󠄐󠄹󠅀󠄪󠄡󠄨󠄞󠄡󠄨󠄨󠄞󠄡󠄦󠄣󠄞󠄢󠄣󠄦󠄬󠅒󠅢󠄟󠄮󠄐󠅅󠄹󠄴󠄪󠄾󠅟󠅤󠄐󠄼󠅟󠅗󠅙󠅞󠄬󠅒󠅢󠄟󠄮󠇘󠆭󠆘󠇙󠆝󠅵󠇗󠆭󠆁󠄐󠇗󠅹󠅸󠇖󠆍󠅳󠇖󠅹󠅰󠇖󠆌󠅹󠄬󠅒󠅢󠄟󠄮
作者:周清跃,田常海,张银花,刘丰收,陈朝阳,俞 喆(中国铁道科学研究院金属及化学研究所,北京 100081)󠄐󠄹󠅀󠄪󠄡󠄨󠄞󠄡󠄨󠄨󠄞󠄡󠄦󠄣󠄞󠄢󠄣󠄦󠄬󠅒󠅢󠄟󠄮󠄐󠅅󠄹󠄴󠄪󠄾󠅟󠅤󠄐󠄼󠅟󠅗󠅙󠅞󠄬󠅒󠅢󠄟󠄮󠇘󠆭󠆘󠇙󠆝󠅵󠇗󠆭󠆁󠄐󠇗󠅹󠅸󠇖󠆍󠅳󠇖󠅹󠅰󠇖󠆌󠅹󠄬󠅒󠅢󠄟󠄮
[/reply]󠄐󠄹󠅀󠄪󠄡󠄨󠄞󠄡󠄨󠄨󠄞󠄡󠄦󠄣󠄞󠄢󠄣󠄦󠄬󠅒󠅢󠄟󠄮󠄐󠅅󠄹󠄴󠄪󠄾󠅟󠅤󠄐󠄼󠅟󠅗󠅙󠅞󠄬󠅒󠅢󠄟󠄮󠇘󠆭󠆘󠇙󠆝󠅵󠇗󠆭󠆁󠄐󠇗󠅹󠅸󠇖󠆍󠅳󠇖󠅹󠅰󠇖󠆌󠅹󠄬󠅒󠅢󠄟󠄮
值得学习
赞
赞